Grinding
“VEGA” Porous Vitrified Bond Wheel for Wafers Finishing Grinding

Higher surface roughness realized by intermediate processing and final processing of SiC and GaN wafers
- Higher surface roughness is realized by the combination of ultra-fine diamond abrasive grains and vitrified bonds of large and fine porous combination structure.
- Spontaneous blade generation is realized and cutting quality is maintained by bonds
“Taffair” Porous Metal Bond Wheel for Compound Semiconductor Wafers
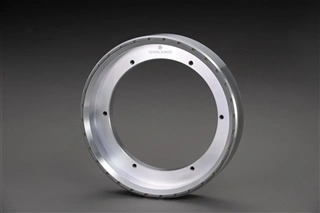
High grinding performance and long tool life for processing of sapphire or SiC wafers
- The porous structure of metal bonds improves biting for higher grinding performance and enhances heat dissipation for longer tool life.
- Not only abrasion resistance of highly rigid metal bonds but also maintaining of cutting quality by appropriate spontaneous blade
“Metarex” diamond wheels for high-efficient grinding of difficult-to-cut materials

These metal bond wheels are designed with a new concept, and have both the high cutting performance of resin bonds and the abrasion resistance of metal bonds. They are suitable for efficient grinding of difficult-to-cut materials such as Al2O3-TiC and quartz
Diamond wheels for edge grinding (beveling) semiconductor wafers
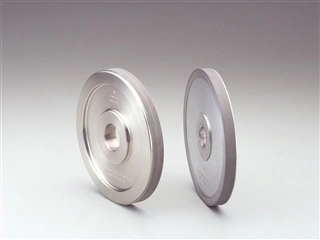
This wheel is used for edge grinding (beveling) semiconductor wafers.
We offer “ME” bond for wheels for chamfering silicon wafers with excellent sharpness and high maintenance of groove shape. The finished surface roughness is excellent, and the amount of polishing after chamfering is reduced, leading to lower total processing costs by reducing the post-process time and consumables.
Diamond notch wheel for semiconductor wafers

This wheel is used for chamfering and finishing the notch of semiconductor wafers. The runout accuracy of the diamond layer to the shank is excellent due to our original processing technology. In addition to silicon wafers, we also provide wheels with various specifications for compound semiconductor wafers such as SiC (silicon carbide) and LT (lithium tantalate), which are becoming larger nowadays, and for quartz wafers.
Diamond multi-layer wheels

A single wheel of this type can perform multiple grinding processes such as rough grinding, pre-finishing, and finishing. This allows multiple processes to be performed with a single machine without replacing tools, which reduces processing time. Multi-layer wheels with a combination of metal bonds for rough grinding, resin bonds for pre-finishing, and resin bonds for finishing are available.
Electroplated pad conditioning dresser for semiconductor polishing pad

This wheel is used for dressing/conditioning the polishing pads used in the flattening process of semiconductor devices.
Electroplated the appropriate abrasive grains of the selected diamond to a base metal brings stable dressing/conditioning, and results in reduced individual differences.
Diamond core drill

Diamond core drills were originally designed for drilling and coring of hard and brittle materials, but their use is now expanding to include the shape machining of hard materials such as ceramics on machining and gliding centers.
The coolant is supplied with a center-through structure, which allows chips to escape easily and reduces damage to the tool and workpiece caused by the chips, thus enabling highly efficient machining.
This tool is ideal for spot facing by helical grinding in narrow widths where chips tend to accumulate.
We offer the most suitable shape for high-efficiency drilling of glass and ceramics.
The strong bond bridge structure ensures long life and stable cutting performance
Diamond wheel for surface grinding of hard brittle materials
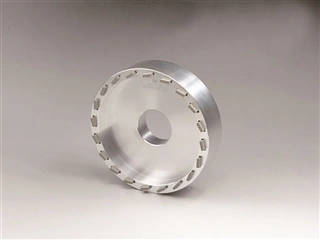
This wheel is designed for surface grinding of electronic or semiconductor materials such as ceramics, quartz, and sapphires. The “”G2(G square)”” porous vitrified bond ensures high cutting performance and efficient, precision grinding can be achieved
if the wheel is combined with special segment shapes.
Diamond wheel for forming hard brittle materials
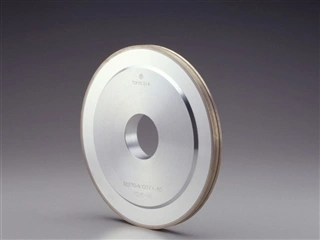
The “MF50” metal bond wheel is used for fine ceramics forming, glass substrate chamfering, and the forming of other hard brittle materials. Its advantages include high cutting performance and low grinding noise.
Diamond pellet wheel for surface grinding of hard brittle materials
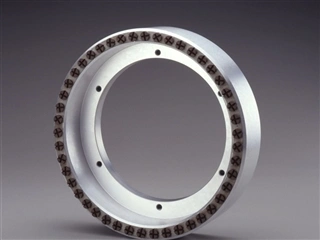
This wheel takes full advantage of aligned pellets for large-area surface grinding of materials such as quartz and ceramics in situations where flatness and cutting performance are required. Various pellet shapes and bonds are available to meet material features and wheel usage requirements.
Diamond wheels for mirror finishing of difficult-to-cut materials

“BL” porous resin bond wheels are designed for mirror grinding of cemented carbide / tungsten carbide molds, ceramics, silicon wafers, and hardening steel alloys. With the effect of pores and a heat-resistant bond strengthened by special filler, these wheels produce high quality finished surfaces while maintaining their cutting performance.
Large Size Resin Bond Wheel

- Single-piece formation of a resin bond wheel with a maximum outer diameter of φ600mm and width of T100mm can be realized.
- Grinding trace at joint is eliminated.
- Dynamic balance of 0.1μm is realized for products with a dedicated flange.
“DEX” diamond wheels for chamfering glass disks
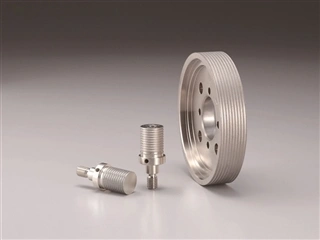
These wheels are used to chamfer the inner diameter (ID) or outer diameter (OD) edge of glass disks. Due to the special electroplating used in this design, the roughness of chamfered surfaces are improved and chipping at the boundary area to the edge surface is minimized. Wheels using micron size abrasive grain are available.
“DEX” diamond wheels for forming difficult-to-cut materials
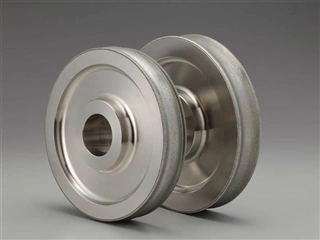
These wheels are designed for high shape precision forming of, for example, motor cores. Wheels of the most appropriate specifications are available for not only magnetic materials such as neodymium-iron, but also for ferrites, ceramics and glass.
“DEX” diamond wheel for high-efficiency milling of difficult-to-cut materials

This wheel enables deep milling of difficult-to-cut composite fiber materials such as brake linings, architectural ceramic materials, secondary products of cement, carbon, FRP, and thermoset resins. The amount of ground material removed per unit time is relatively large, which realizes highly efficient grinding. By controlling the contact area between the material being ground and the wheel, this design reduces grinding noise, suppresses additional electric current in the main spindle, and contributes to energy saving.
“DEX” diamond wheel for optical lens centering
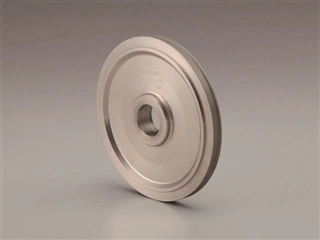
It is useful for aligning the optical axis (centering) of lenses that require high precision, such as aspheric lenses and steppers that are the heart of high-end cameras and endoscopes. It does not require break-in processing, and it is possible to manufacture lenses that have reduced sharpness and chipping on the lens edge from the start of processing, and it suppresses lens burns even for shapes with sharp edges.
“Metalist” CBN Metal Bond Wheel for Iron Material

“Metalist” CBN Metal Bond Wheel for Iron Material
- The product not only maintains cutting performance and realizes long tool life, but also suppresses burning of work materials.
- Since it can suppress heat stress on work materials more than conventional abrasive wheels, reduction of the fatigue-resistant strength of the work can be suppressed.
- Little damage on abrasive grains and appropriate spontaneous blade generation can realize long dress intervals and reduce down time.
[Target materials for CBN metal bond wheels]
– HSS (High-Speed Steel)
– Hardened Steel (carbon steel, die steel)
CBN wheels for grinding iron materials

These wheels realize high-precision grinding of iron materials used for automobile parts and the like. They provide the advantages of high performance and stable quality. CBN wheels with an axis are also available.
“CITIUS” diamond wheels for heavy grinding of carbide tools
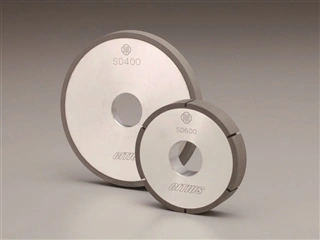
These wheels demonstrate their distinguished performance for deep-gutter flute grinding of cemented carbide / tungsten carbide tools. Compared to conventional resin bond wheels, they reduce machining time and abrasion. They also achieve stable cutting performance, high-precision, and high-quality surface roughness, and reduce the generation of chips. “BI30” and “MB” series resin bond wheels are also available depending on the materials to be ground and on usage.
“High-RESPONSE” diamond wheels for grinding PCD/PCBN tools
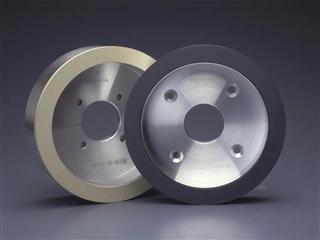
These wheels are used for grinding PCD and PCBN tools, which have higher hardness, higher strength and higher abrasion resistance than carbide tools. Two (non-porous and porous) “high-RESPONSE” bond types are available to meet customer needs for higher precision and higher efficiency.
CBN wheel for heavy grinding of high-speed tools
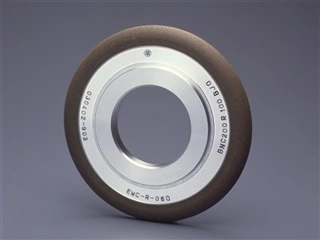
The highly durable “BJ0” resin bond wheel is useful for flute grinding of high-speed drills and taps. It has low grinding resistance in creep feed grinding of high-speed steel, thus maintaining its high cutting performance.
Diamond mounted wheels for glass lens mold machining

Diamond mounted V-face wheels are tools mainly used for aspherical surface machining of glass lens molds.
For plastic lens molds, nickel is machined with an ultra-precise single-crystal diamond cutting tool, while ultra-fine binderless cemented carbide is used for glass lens molds. In addition, demand for SiC molds has been increasing recently.
For the machining of such binderless cemented carbide and SiC lens molds, grinding with a diamond wheel with shaft is used because cutting with a single-crystal diamond cutting tool is unsuitable and inefficient.
We have extensive experience with single-crystal diamond cutting tools for plastic lens molds, and also offer various specifications of diamond mounted wheels for glass lens mold machining.
In addition to V-face shaft wheels, we also offer cylindrical small-diameter shaft wheels for diagonal grinding, free-form grinding, dressing, and sleeve mold machining.